Back to blog list
How AI Empowers Distributors’ Quality and Compliance Teams: A CoA Perspective
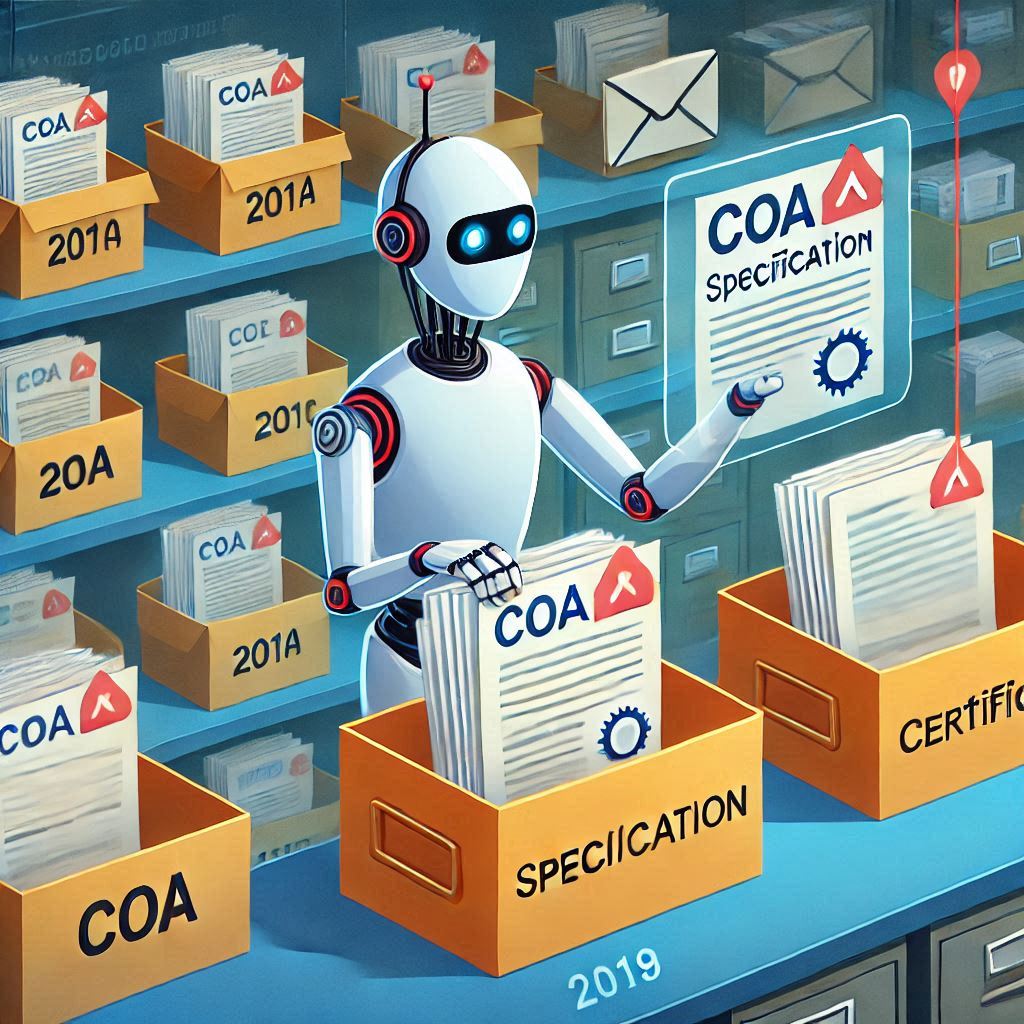
Summary: Certificates of Analysis (CoAs) documents show that a product meets predetermined quality standards. Many distributors still manage CoAs manually, which is time-consuming, error-prone, and risky in terms of compliance and customer satisfaction. AI-driven solutions, like those from UpBrains AI, automate document processing, validation, and tracking, drastically reducing errors and administrative burdens. This allows Quality and Compliance Teams to focus on strategic initiatives rather than paperwork management.
Introduction
In an era where safety, transparency, and regulatory compliance are paramount, distributors in industries such as chemical, food, and pharmaceuticals face increasing pressure to accurately manage and provide key quality documents. Among these documents, the Certificate of Analysis (CoA) stands out as an essential validation of product quality and integrity. Yet, for many organizations, the process of acquiring, organizing, verifying, and delivering CoAs is still largely manual—leading to inefficiencies, risks, and high operational costs. This article unpacks the importance of Certificates of Analysis, the challenges of managing them in a traditional manner, and how AI-powered solutions can revolutionize the process.
What Is a Certificate of Analysis?
A Certificate of Analysis (CoA) is a document issued by a product’s manufacturer that certifies that the product meets its predetermined quality standards and specifications. In simple terms, a CoA verifies that the product in question has undergone specific tests or analyses and that its results fall within the acceptable range outlined by regulatory agencies or internal quality standards.
Key Components Typically Found in a CoA
Product Identification: Name, grade, or other identifying attributes of the product.
Supplier or Manufacturer Information: Contact details and location of the issuing manufacturer.
Lot Number or Batch Number: A unique identifier tracing the product to a specific production batch.
Test Parameters and Methods: Analytical tests performed, such as purity, potency, microbial limits, or chemical composition.
Test Results: Measured values or results that are compared against acceptable specification ranges.
Signatures and Dates: Validation by an authorized quality representative and the date the CoA was issued.
Who Issues the CoA, and Who Manages It?
Manufacturers Issue the CoA
The manufacturer of a product, whether it is a chemical compound, a food additive, or a pharmaceutical ingredient, is typically responsible for issuing the CoA. This document serves as proof that the lot or batch they produced meets the relevant specifications. Manufacturers employ rigorous quality control processes—often under the guidance of internal quality specialists and external regulatory requirements—to ensure products adhere to consistent standards before distribution.
Distributors’ Quality and Compliance Teams Manage CoA
After the manufacturer issues the CoA, distributors receive these documents along with the product shipments they purchase for resale. Within these distribution companies, Quality and Compliance Teams are tasked with managing the CoA and other certification documents. Their responsibilities include:
Collecting CoAs from Suppliers: Ensuring each lot they procure comes with a valid, up-to-date Certificate of Analysis.
Organizing by Supplier, Product, and Lot Number: Categorizing these documents so they are easy to retrieve when needed.
Monitoring Expiry Dates: Certificates may have validity windows, especially for products with a specified shelf life or for time-sensitive quality parameters.
Responding to Client Requests: Clients may ask for specific documents (CoAs, Halal Certificates, Kosher Certificates, etc.) before or after purchase.
Verifying Content and Accuracy: Ensuring that the data in each CoA is valid and that the product indeed meets all the required specifications.
The Importance of Keeping Track of CoAs and Related Certificates
When a distributor receives bulk quantities from different suppliers, each product lot or batch will have a separate CoA. Properly maintaining these CoAs is crucial for:
Regulatory Compliance: Regulatory agencies often audit distributors to ensure they have the correct documentation for every product lot they handle.
Safety Assurance: A verified CoA confirms that the product has passed essential safety checks. This is especially critical in pharmaceutical and food industries.
Traceability: In the event of a recall or customer complaint, quickly identifying which lots were affected can significantly reduce liability and harm.
Building Trust: Providing timely, accurate CoAs to clients promotes transparency and reinforces the distributor’s commitment to quality.
Challenges of Manually Handling CoA Documents
Despite the importance of CoAs, many distributors still manually manage these critical documents. This can create a range of operational and compliance problems, including:
Data Entry Errors: Entering CoA details into spreadsheets or legacy systems by hand is time-consuming and prone to human error.
Misplaced or Lost Documents: Physical files or chaotic digital folders can easily go missing, especially if multiple people handle them.
Difficulty in Tracking Expiry Dates: Certificates often have time-sensitive information; manually tracking numerous documents increases the likelihood of oversight.
Delayed Responses to Clients: When customers request CoAs or other certificates, manual retrieval can lead to delays. This could negatively impact customer satisfaction and even delay product releases.
Inaccurate Verification: Quality and Compliance Teams are often too busy reacting to urgent issues to thoroughly verify each new CoA. This reactive approach can lead to overlooking critical quality discrepancies until a serious incident—like a health or safety issue—arises.
Inconsistent Updates: When a product specification changes or a new version of the CoA is released, manually updating every record is tedious and prone to lapses.
The outcome of these challenges is a high-risk environment where compliance failures can be costly—in terms of fines, brand reputation, and customer trust. Manual processes also eat up valuable time and resources, distracting teams from strategic quality and compliance planning.
How AI Can Transform CoA and Quality Documentation Management
The good news for distributors is that Artificial Intelligence (AI) is poised to dramatically improve how CoAs and other compliance documents are handled. AI technologies—especially those focusing on intelligent document processing—offer several game-changing benefits:
1. Automated Document Intake
AI can scan and read incoming CoA documents—whether they arrive via email attachments or digital portals—and extract key details such as product name, supplier, lot number, expiry date, and test results. This eliminates the bulk of the manual data entry work, freeing teams to focus on higher-value tasks.
2. Intelligent Categorization and Organization
Once the key information is extracted, the AI system can automatically categorize and store the documents by supplier, product type, and lot number. This ensures that the right information is always at the teams’ fingertips—when a client calls or a regulatory authority stops by.
3. Validation and Verification
With the right rule-based or machine learning models, AI can validate test results against specified ranges and flag any anomalies. If a particular lot has a parameter out of range or a missing signature, the system can alert the Quality and Compliance Team proactively.
4. Alerts for Document Renewal or Expiration
By tracking the expiry or review dates for each CoA, AI can send automated reminders when a renewal is due, significantly reducing the chance of using expired or outdated documents.
5. Streamlined Client Inquiries
For distributors that frequently receive requests for CoAs, Halal Certificates, Kosher Certificates, or other product-specific documentation, AI can help by:
Identifying the requested documents in the system
Automatically retrieving them based on supplier or lot number
Responding to clients with relevant attachments or links in a fraction of the time it would take a human to do so manually
6. Centralized Dashboard and Reporting
An AI-driven solution can offer a real-time dashboard displaying CoA status, upcoming expirations, and flagged compliance issues. It can also generate reports for audits or internal reviews, giving management immediate insight into the state of quality documentation across the organization.
Introducing UpBrains AI's Expert Agents for Quality Documentation
Many organizations have begun looking for end-to-end AI platforms that can comprehensively handle compliance and quality documentation processes. UpBrains AI stands out by providing a suite of expert agents specializing in:
Certificate of Analysis Management
Compliance and Quality Document Processing
Certification Documents (e.g., Kosher, Halal, Organic, etc.)
Intelligent Agent for Quality Team Inbox Management
Together, these agents form a robust AI-driven ecosystem that streamlines tasks, reduces errors, and offers proactive solutions for Quality and Compliance Teams. Here’s what you can expect from the UpBrains AI platform:
Seamless Integration: The platform can integrate with email inboxes, ERP systems, and supplier portals to receive new CoAs automatically.
Automated Parsing: Expert algorithms read and extract critical data, significantly reducing manual input and minimizing errors.
Proactive Alerts: When documents are about to expire or if a test result is out of specification, the relevant team members receive immediate notifications.
Client Inquiry Support: An intelligent agent manages client requests, pulling the necessary documents from the archive without human intervention.
Compliance Dashboard: At-a-glance visibility into all your documentation’s status, with detailed drill-down capabilities for deeper investigations.
Scalability and Adaptability: As your product lines expand, the solution scales without increasing the burden on your Quality and Compliance Team.
Focus on What Matters Most: Strategic Quality and Compliance
The ultimate advantage of automating CoA and certification document management lies in freeing your Quality and Compliance Team from tedious, repetitive tasks. Instead of pouring hours into administrative document handling, they can:
Proactively Plan for Quality: Devote time to improving quality standards and exploring new certifications that offer market differentiation.
Strengthen Regulatory Strategies: Stay ahead of evolving regulatory demands in the chemical, food, and pharmaceutical industries.
Build Stakeholder Confidence: Deepen relationships with clients, suppliers, and regulatory bodies by demonstrating consistent and reliable documentation management.
Drive Continuous Improvement: Channel resources into system improvements, staff training, and strategic initiatives that reduce overall risk.
Conclusion
Manually managing Certificates of Analysis (CoAs) and related quality documentation has become unsustainable and risky in a fast-paced, highly regulated environment. From the initial ingestion of CoAs to validation, renewal tracking, and client distribution, every step is crucial to ensuring product safety, regulatory compliance, and customer satisfaction. AI-driven solutions, such as those offered by UpBrains AI, bring unprecedented efficiency, accuracy, and scalability to these processes.
By leveraging intelligent agents for CoA management, certification document handling, and proactive alerts, distributors can move from a reactive and error-prone system to a proactive, cost-effective, and transparent operation. The result? Higher confidence in product quality, faster client responses, reduced compliance risks, and more bandwidth for strategic initiatives that truly elevate your brand and bottom line.
Ready to Transform Your CoA Management?
Discover how UpBrains AI can revolutionize your approach to Certificate of Analysis and compliance documentation. Move beyond manual workflows and embrace an automated, intelligent future that empowers your Quality and Compliance Teams to excel where it matters most.
Explore other articles
See all blogs